2024 Manufacturing Trends: Key Innovations and Challenges Shaping the Industry
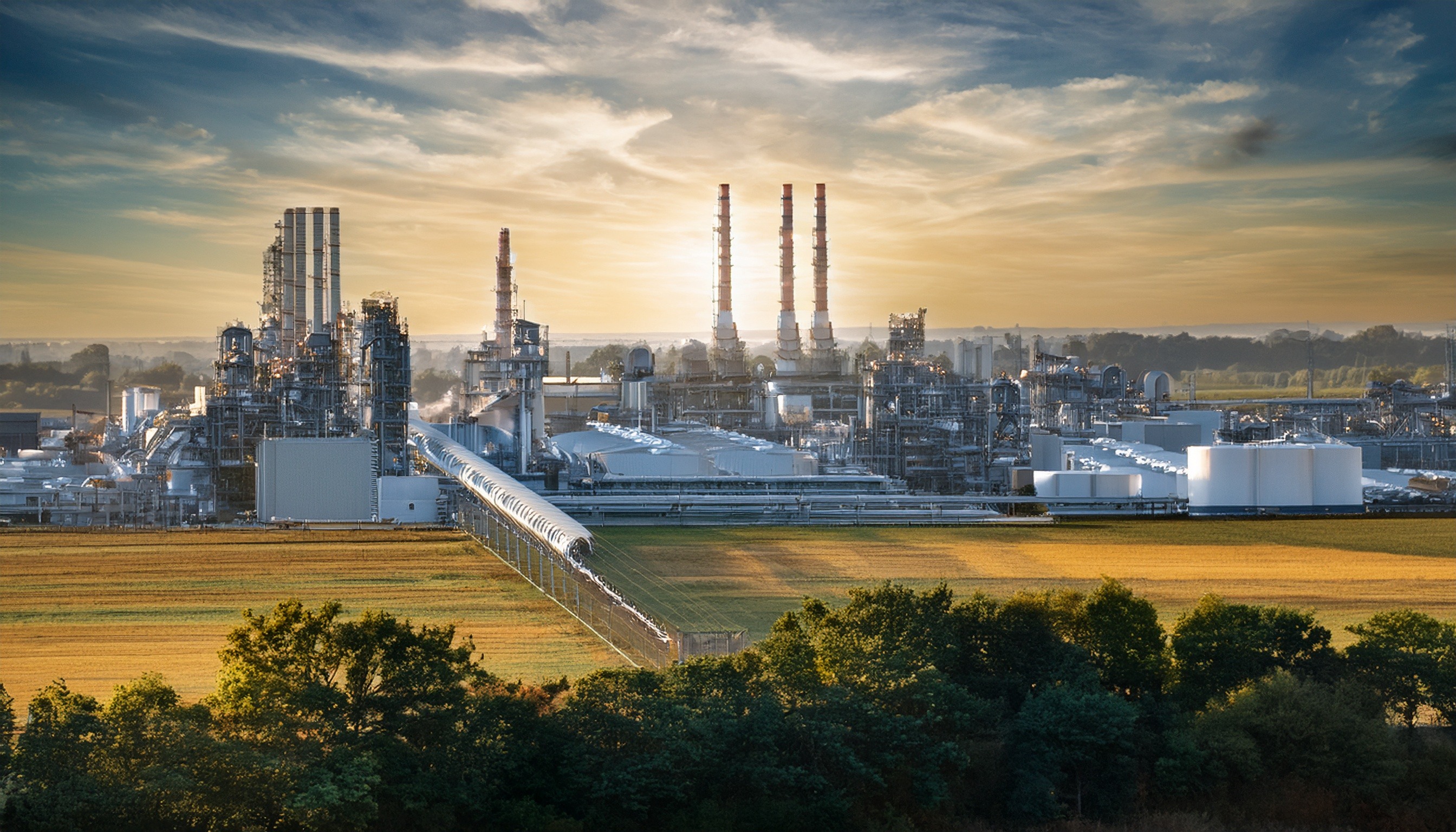
The manufacturing industry is in the midst of a significant transformation, driven by rapid technological advancements, global economic shifts and evolving consumer demands. Staying informed about these changes is no longer optional but critical for maintaining a competitive edge.
As we look back on 2024, three themes dominate the manufacturing landscape: innovation, resilience and adaptability. Whoever manages to balance those tasks on top of rising challenges, such as sustainability and talent shortages, will see the best results going into 2025.
Why Staying Current With Trends in the Manufacturing Industry Matters
Manufacturing is a dynamic sector, and as such, it demands greater efficiency every day. For most manufacturing enterprises, falling behind on trends can have serious repercussions. Businesses that fail to adopt emerging technologies risk reduced operational efficiency, diminished competitiveness and long-term profitability challenges.
That’s if you don’t consider the ripple effects through the global supply chain and their impact on customer experience and labor statistics in an increasingly connected world. Conversely, those who act early on a trend often gain a significant advantage, be it through advanced supply chain management or industrial automation.
For instance, a plastics manufacturing systems provider partnered with The TM Group to implement a modernized solution, resulting in enhanced efficiency and supply chain resilience. Such examples highlight the tangible benefits of aligning with industry trends and the risks of inaction.
Key Manufacturing Trends in 2024
Many of the same news buzzwords have remained the same in 2024, but the political and legal landscape has changed, and the nuanced approaches to these challenges have drastically evolved. So it’s worth looking at the details of recent manufacturing industry trends.
Labor Challenges and Talent Wars
The manufacturing sector continues to grapple with workforce shortages, particularly in skilled technical roles. Demand for expertise in simulation software has surged by 75% over the past five years, while industrial machinery maintenance technicians are expected to see a 16% demand growth by 2032. In the U.S., labor shortages hover at 70%, just below the global average. To address the labor shortage and leverage opportunities that advanced technology promises, 71% of enterprises are investing in upskilling and reskilling programs.
It’s also worth pointing out that talent wars don’t affect the entire manufacturing sector equally. Most manufacturing leaders certainly see similar patterns, but some industries face acute challenges. 47% of construction sector respondents strongly agree they’re experiencing labor shortages, followed closely by aerospace and defense (45%). Automation offers some relief, but job displacement concerns necessitate comprehensive reskilling initiatives to help workers transition into roles within smart manufacturing environments.
Predictive and Data-Driven Decision Making
Smart sensors and IoT technologies are redefining the "factory of the future." Advanced data analytics enables manufacturers to predict equipment failures, reduce waste and optimize production. Research comparing random forest models with other machine learning techniques underscores the potential of predictive technologies to improve operational outcomes. It’s safe to say that in-depth research like this will continue to shape industry-specific applications.
Even now, these advancements aren’t just theoretical. Companies adopting data-driven strategies report higher productivity and reduced downtime, showcasing the transformative power of analytics.
Cybersecurity in Manufacturing
As manufacturers rely more on connected devices and digital systems, cybersecurity risks have intensified. Recent incidents, such as a cyberattack that exposed 40 GB of critical data, emphasize the vulnerabilities in manufacturing ecosystems. Another attack targeting a software firm disrupted thousands of U.S. car dealerships, highlighting the risks of vendor dependency.
To mitigate these threats, manufacturers must adopt robust security measures, such as multi-factor authentication and regular system audits, to safeguard intellectual property and operational continuity.
Smart Supply Chains
Global crises and geopolitical tensions have underscored the importance of resilient supply chains. Technologies like blockchain, artificial intelligence (AI) and the Internet of Things (IoT) are helping manufacturers enhance visibility, reduce inefficiencies and improve adaptability.
For example, IoT-enabled data collection has led to a 3% reduction in energy usage and a 4% cost reduction in some industrial processes. Furthermore, 33% of revenue from smart products — expected to rise to 47% within three years — demonstrates the financial benefits of adopting innovative supply chain strategies.
The critical challenges in achieving those results often lie in overcoming data transmission delays, data throughput bottlenecks and data gathering reliability issues. As software solutions grow more complex, manufacturers need to invest more time in options tailored to their specific environments and niche challenges, paired with expert support for an individualized setup.
Sustainability and Carbon Neutrality
Sustainability is no longer a choice but a mandate. Manufacturers are turning to renewable energy and initiatives to reduce their carbon footprints. Advanced forecasting models have decreased error rates by over 50%, improving process efficiency and aligning production with sustainability goals. Green financial inclusion initiatives and renewable energy adoption will shape the next decade of manufacturing, even though the coordination of initiatives around the globe will remain a challenge.
3D Printing and Additive Manufacturing
The global 3D printing market, valued at $16.75 billion in 2022, is projected to grow at a 23.3% CAGR through 2030. This technology enables rapid prototyping, mass customization and waste reduction. Notable applications include biomedical implants, aerospace components and even lunar habitat construction using 90% lunar raw materials.
Even though certain challenges such as part size and mass customization remain, additive manufacturing has already shown tremendous value in fields like biomedical applications, aerospace and the automobile industry. As costs drop and speeds increase, 3D printing’s potential will only expand.
Robotics and Automation
Advanced robotics are helping manufacturers address labor shortages and boost efficiency. These systems can handle complex tasks with precision, increasing productivity and minimizing human error. Automation is a critical strategy for companies aiming to stay competitive in a tight labor market.
While robotics do come with significant promises across industries, the initial acquisition costs usually don’t include integration management or maintenance costs. As we approach 2025, each manufacturer needs to evaluate the standards and existing infrastructure in their setup to assess whether implementing different automation solutions is worth the investment.
Servitization
Manufacturers are shifting from a product-centric model to a service-oriented approach, bundling maintenance, upgrades and other value-added services. Some companies now earn over 50% of their revenue from servicing equipment, illustrating the profitability of this transition.
Emerging Technologies: XR and Digital Twins
Extended reality (XR) and digital twins (DTs) are becoming essential tools for training, prototyping and maintenance.
As the cost for DTs decreases, they will likely replace 3D visualization, synchronized transmission and monitoring interaction technologies for many manufacturers, thus further reducing time-to-market and optimizing plant equipment.
DTs already enable real-time monitoring and predictive maintenance, while XR facilitates immersive training experiences. What’s certain is that both technologies will drive more advanced engineering in the Metaverse. The challenge that still remains unanswered is how different industries can develop and agree on a systematic method to achieve synergies between the two.
Challenges Facing Manufacturing Companies in 2025
Retaining skilled workers remains a top concern, and as it relates to countless developments from technological advancements to the political landscape, it will likely remain an ongoing discussion in 2025.
Outdated perceptions of manufacturing jobs as monotonous deter younger talent. To combat this, companies must offer competitive salaries, invest in employee development and embrace technology to redefine industry perceptions.
Industry experts also recommend creating a feedback-friendly environment and using AI to unify data from different sources to allow for real-time data updates.
Uncertainty in trade policies and global economic conditions also creates challenges for manufacturers. Developing flexible supply chains and diversifying markets can help mitigate these risks.
With increasing digitalization, robust cybersecurity measures are essential to prevent breaches and protect sensitive data. In fact, 69% of surveyed manufacturing decision-makers mentioned lack of expertise as a major factor preventing digitalization at their company. The fast pace of innovation can overwhelm businesses, and implementing new technologies without disrupting operations requires strategic planning and phased rollouts.
The Future Outlook for the Manufacturing Sector
Whether it’s AI or talent wars, last year’s challenges will carry over well into 2025 and beyond, forcing manufacturers to constantly adapt their strategies, from talent retention to technological innovation.
Over the next decade, automation, sustainability and advanced technologies will continue to reshape manufacturing, even though not each advancement will make big headlines, as innovators are tackling more niche challenges. Adaptability and proactive planning will be critical for businesses to stay ahead of the curve. Companies that prioritize innovation and resilience, choosing strategic partnerships for support, will thrive in this evolving landscape.
Is Your Manufacturing Business Ready for the Future?
Staying informed and adopting emerging trends is crucial for navigating the complexities of modern manufacturing. Evaluate your readiness to tackle these trends and challenges. Take note of everything that went well in 2024, as well as everything that could have gone better.
If you’re willing to enter the next level and finally advance your operations, partner with experts like The TM Group to navigate 2025’s manufacturing landscape. Whether you're optimizing your current setup or exploring a new ERP system, our team can guide you every step of the way. Reach out to our team today to learn about Microsoft Dynamics 365 Business Central.